Petroleum Laboratory
Forms
Important: Download and save a copy of the form(s) you need and enter your information in the saved copy instead of typing in the form that appears in the browser window.
About the State Fuel Quality Laboratory
The Fuel Quality Laboratory analyzes diesel, gasoline and ethanol fuel blend samples from all fuel dispensing facilities in the State of Colorado to ensure compliance with all federal, state and local statutes and regulations.
For frequently asked questions (FAQ), visit the FAQ website.
Gasoline and Ethanol Fuel Blend Analyses and Specifications
[Last revised date 01/23/2025]
The State Fuel Quality Laboratory performs six American Society of Testing and Materials (ASTM) approved analyses on each gasoline sample received from retail stations and bulk plants located throughout the State of Colorado. In addition, the Laboratory assesses the quality of gasoline fuels in response to consumer concerns (Consumer Concern Form). All gasoline fuels are sampled, handled and stored in accordance with ASTM D4840-99 and ASTM D4057-22.
All grades of unleaded gasoline must meet the requirements set forth in ASTM D4814-24a. The fuels covered by this standard are gasoline and its blends with oxygenates, such as alcohols and ethers (including Reformulated Gasoline). Fuels containing ethanol as the primary component (e.g., E85) must meet the requirements described in ASTM D5798-21. These standards define the seasonally changing properties that automotive fuels must have throughout the year in order to provide the best performance under varying operating conditions.
The analyses and calculations performed at the State Fuel Quality Laboratory are explained in the collapsible sections below.
To fulfill all essential quality requirements, the State Fuel Quality Laboratory has implemented and routinely performs a variety of Quality Control Checks and Quality Assurance Procedures in accordance with ASTM D6299-23a, ASTM D6792-23c, ASTM E882 and as defined in all ASTM Standard Test Methods. Additionally, the State Fuel Quality Laboratory participates in an International Quality Assurance Exchange Program – an interlaboratory proficiency testing program to evaluate laboratory performances, monitor test methods, personnel and reporting procedures on a monthly basis.
Gasoline’s vapor pressure is the pressure exerted by gasoline vapor in thermodynamic equilibrium with its liquid phase at a given temperature in a closed system. The vapor pressure is an indication of the gasoline’s tendency to evaporate and thus, a very important physical property of volatile gasoline products. Fuels that vaporize too readily in pumps, fuel lines, carburetors, or fuel injectors will cause decreased fuel flow to the engine, resulting in rough engine operation or vapor lock, especially in mountain driving. In contrast, fuel that does not vaporize readily may cause hard starting and poor warm-up drivability and acceleration. The vapor pressure of gasoline fuels (E0, E10, E15) (Table 1) and flex fuel blends (E85) (Table 2) is regulated by various government agencies to ensure fuel products of suitable volatility performance throughout seasonal variations in temperatures.
Table 1 – Vapor Pressure Requirements for Gasoline (E0) and Ethanol-blended Gasoline (E10, E15) within the State of Colorado
Month | Vapor Pressure [pound per square inch, psi] for E0 and E15 | Vapor pressure [pound per square inch, psi] for E101 | EPA's Vapor Pressure Limits [pound per square inch, psi] |
---|---|---|---|
January | 13.5 | 14.5 | |
February | 13.5 | 14.5 | |
March | 11.5 | 12.5 | |
April | 11.5 | 12.5 | |
May | 11.5 | 12.5 | |
June | 9 | 10 | 7.42 |
July | 9 | 10 | 7.42 |
August | 9 | 10 | 7.42 |
September 1-15 | 9 | 10 | 7.42 |
September 16-end | 10 | 11 | |
October | 11.5 | 12.5 | |
November | 13.5 | 14.5 | |
December | 13.5 | 14.5 |
EPA: Environmental Protection Agency
1The listed vapor pressure requirements include a 1.0 psi higher vapor pressure for conventional gasoline-ethanol blend containing 9-10% as granted by Colorado Revised Statutes. (Reformulated gasoline is strictly excluded from this 1.0 psi waiver during the ozone season (June-September 15) in the ozone nonattainment area.)
2This maximum vapor pressure at 37.8 °C (100 °F) for Reformulated Gasoline is required in the severe ozone nonattainment areas (Adams, Arapahoe, Boulder, Broomfield, Denver, Douglas, Jefferson, parts of Larimer and Weld counties) and is called reformulated gasoline. Figure 1 depicts the severe ozone nonattainment areas in which these specific vapor pressure limits have to be met to improve air quality.
Figure 1 - Severe Ozone Nonattainment Area in Colorado
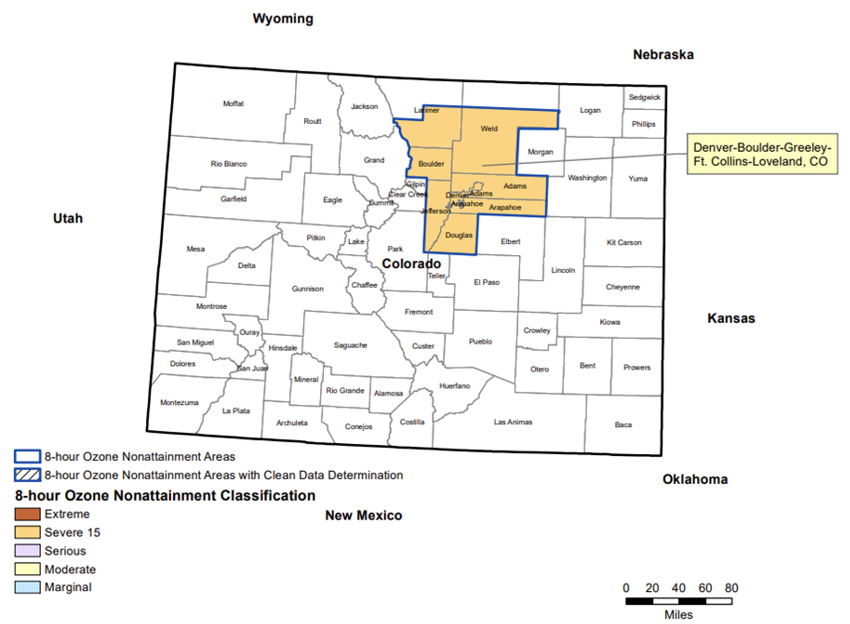
Table 2 – Vapor Pressure Requirements for E85 Flex Fuel Blends (containing 51-83% ethanol) within the State of Colorado]
Vapor Pressure [psi, pound per square inch] | ||
---|---|---|
Month | East of 105° Longitude | West of 105° Longitude |
January | 9.5-15.0 | 9.5-15.0 |
February | 8.5-15.0 | 9.5-15.0 |
March | 8.5-12.0 | 8.5-12.0 |
April | 7.0-12.0 | 8.5-12.0 |
May | 7.0-9.5 | 7.0-12.0 |
June | 5.5-9.0 | 7.0-9.5 |
July | 5.5-9.0 | 5.5-9.5 |
August | 5.5-9.0 | 5.5-9.5 |
September | 5.5-9.5 | 7.0-12.0 |
October | 7.0-12.0 | 8.5-15.0 |
November | 8.5-12.0 | 9.5-15.0 |
December | 8.5-15.0 | 9.5-15.0 |
Note: See Figure 2 for a 105° Longitude Map
Figure 2 - Colorado’s East and West of 105° Longitude
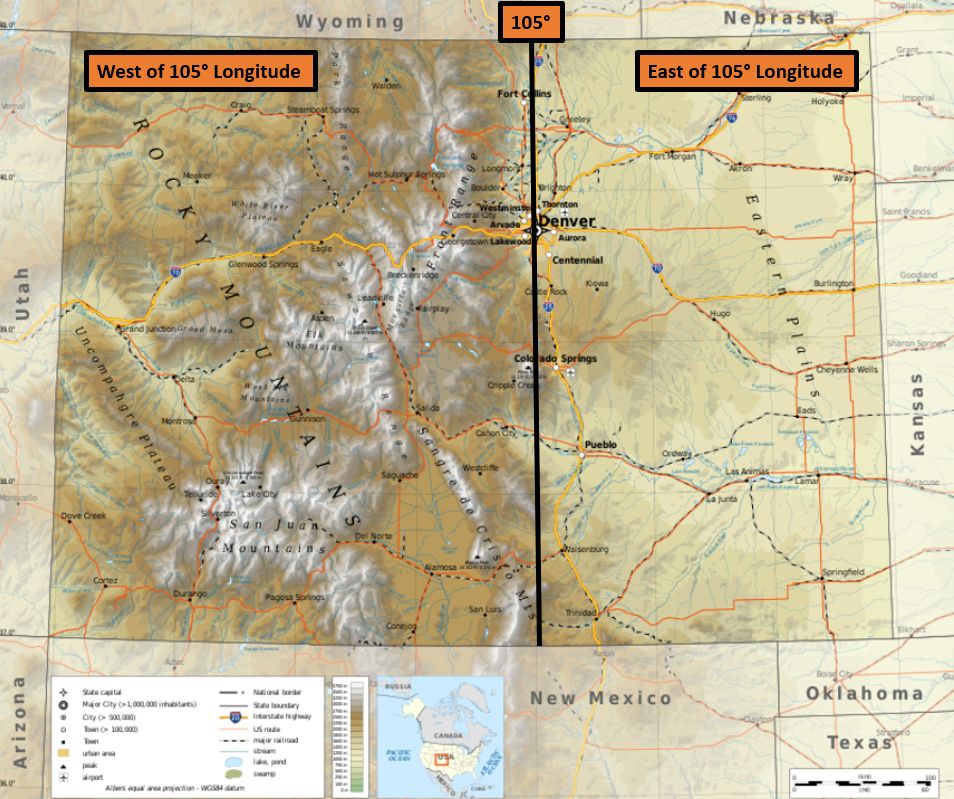
The Colorado State Fuel Quality Laboratory follows ASTM D5191-22, in which a chilled sample is introduced into a thermostatically controlled, evacuated test chamber (see Figure 3). The test specimen is then allowed to reach thermal equilibrium at the test temperature, 37.8 °C (100 °F). The resulting rise in pressure in the chamber is measured using a pressure transducer sensor and indicator.
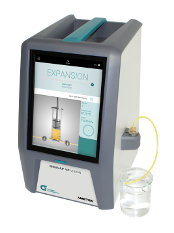
Figure 3 – Automated Vapor Pressure Instrument used at the Colorado State Fuel Quality Laboratory for the determination of the gasoline’s vapor pressure
The vapor-liquid ratio of fuel indicates the tendency of a fuel to vaporize in automotive engine fuel systems. This ratio is the temperature at which gasoline forms a ratio of vapor volume to liquid volume that is equal to 20: T(V/L = 20). Automotive fuel specifications generally include T(V/L = 20) limits to ensure products have a suitable volatility performance. For high temperatures, a fuel with a higher T(V/L = 20) value, which has a lower tendency to vaporize, is specified (Table 1). Conversely, for low temperatures, a fuel with a lower T(V/L = 20) value is specified (Table 1).
Table 1 – Minimum Temperature [°F] for a Vapor/Liquid Ratio of 20.
month | Minimum Temperature [°F] |
---|---|
January | 116 |
February | 116 |
March | 116 |
April | 116 |
May | 116 |
June | 129 |
July | 129 |
August | 122 |
September | 122 |
October | 116 |
November | 116 |
December | 116 |
The Colorado State Fuel Quality Laboratory follows ASTM D5188-23, which covers the determination of the temperature at which the vapor formed from a selected volume of volatile petroleum product (saturated with air at 0 °C to 1 °C (32 °F to 34 °F) produces a pressure of 101.3 kPa (one atmosphere) against vacuum. The instrument used in the Colorado State Fuel Quality Laboratory is depicted in Figure 1.
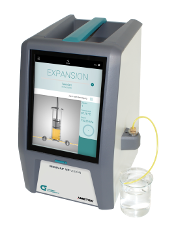
Figure 1 – Automated Vapor Pressure Instrument used at the Colorado State Fuel Quality Laboratory for the determination of the gasoline’s T(V/L = 20)
The test method of determining the boiling range of a petroleum product by performing distillation has been in use for as long as the petroleum industry has existed. It is one of the oldest test methods under the jurisdiction of ASTM. The distillation (volatility) characteristics of hydrocarbons have an important effect on their safety and performance, especially in the case of fuels. The boiling range gives information on the composition, the properties, and the behavior of the fuel during storage and use. Volatility is the major determinant of the tendency of a hydrocarbon mixture to produce potentially explosive vapors. The distillation characteristics are critically important for automotive gasoline and diesel fuels, affecting starting, warm-up, drivability, dilution of the engine oil, fuel economy, carburetor icing and tendency to vapor lock at high operating temperature or at high altitude, or both. The distillation temperatures are used to characterize the volatility of gasoline fuels and to determine whether the distillation properties meet the ASTM specifications (Table 4, Table 5).
Table 4 – Distillation Temperature [°F] Requirements for Gasoline Fuels at Percent Evaporated1
Month | Maximum °F at 10 % | Minimum °F at 50 %2 | Maximum °F at 50 % | Maximum °F at 90 % | Maximum °F at End Point | Maximum Residue [Milliliters] |
---|---|---|---|---|---|---|
January | 131 | 145/150 | 235 | 365 | 437 | 2 |
February | 140 | 140/150 | 235 | 365 | 437 | 2 |
March 1-15 | 140 | 140/150 | 240 | 365 | 437 | 2 |
March 16-end | 140 | 150/170 | 240 | 365 | 437 | 2 |
April | 158 | 150/170 | 250 | 374 | 437 | 2 |
May | 158 | 150/170 | 250 | 374 | 437 | 2 |
June | 158 | 150/170 | 250 | 374 | 437 | 2 |
July | 158 | 150/170 | 250 | 374 | 437 | 2 |
August | 158 | 150/170 | 250 | 374 | 437 | 2 |
September | 158 | 150/170 | 250 | 374 | 437 | 2 |
October 1-15 | 158 | 150/170 | 250 | 374 | 437 | 2 |
October 16-end | 149 | 150/170 | 245 | 374 | 437 | 2 |
November 1-15 | 149 | 145/150 | 245 | 374 | 437 | 2 |
November 16-end | 140 | 145/150 | 240 | 365 | 437 | 2 |
December 1-15 | 140 | 145/150 | 240 | 365 | 437 | 2 |
December 16-end | 131 | 145/150 | 235 | 365 | 437 | 2 |
1at 101.3 kPa (760 mm Hg)
2for E10 and E15 (left) and for E0 (right)
Table 5 – Distillation Temperature [°F] Requirements for
Flex Fuel Blends at End Point
Maximum °F at End Point | Maximum Residue (Milliliters) |
---|---|
437 | 2 |
The Colorado State Fuel Quality Laboratory follows ASTM D86-23a. A 100 mL sample is distilled under prescribed conditions for the specific fuel sample. The distillation is performed in a laboratory batch distillation unit (Figure 1) at ambient pressure. Systematic observations of temperature readings and volumes of condensate are made automatically. The volume of the residue and the losses are also recorded.
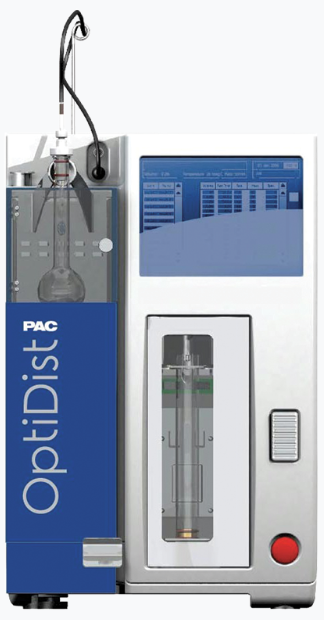
Figure 1 – Distillation Unit used at the Colorado State Fuel Quality Laboratory for the quantitative determination of boiling range characteristics of gasoline fuels
Ethers, alcohols, and other fuel oxygenates can be added to gasoline to increase octane number for greater efficiency and power and to reduce emissions. Types and concentrations of various oxygenates are specified and regulated to ensure acceptable commercial gasoline quality. Drivability, vapor pressure, phase separation, exhaust, and evaporative emissions are some of the concerns associated with oxygenated fuels.
The Colorado State Fuel Quality Laboratory uses ASTM D4815-22 to determine ethanol contents of gasoline samples. However, samples of ethanol fuel blends with high ethanol concentrations (e.g., E85) are analyzed following ASTM D5501-20, and shall contain 51-83 % of ethanol.
In brief summary, a gasoline sample is introduced into a gas chromatograph (Figure 1) equipped with two columns and a column switching valve. The samples are broken down into their components by being washed by a solvent. . The components are then detected by a thermal conductivity detector. The detector response, proportional to the component concentration, is recorded; the peak areas (Figure 2) are measured; and the concentration of each component is calculated.
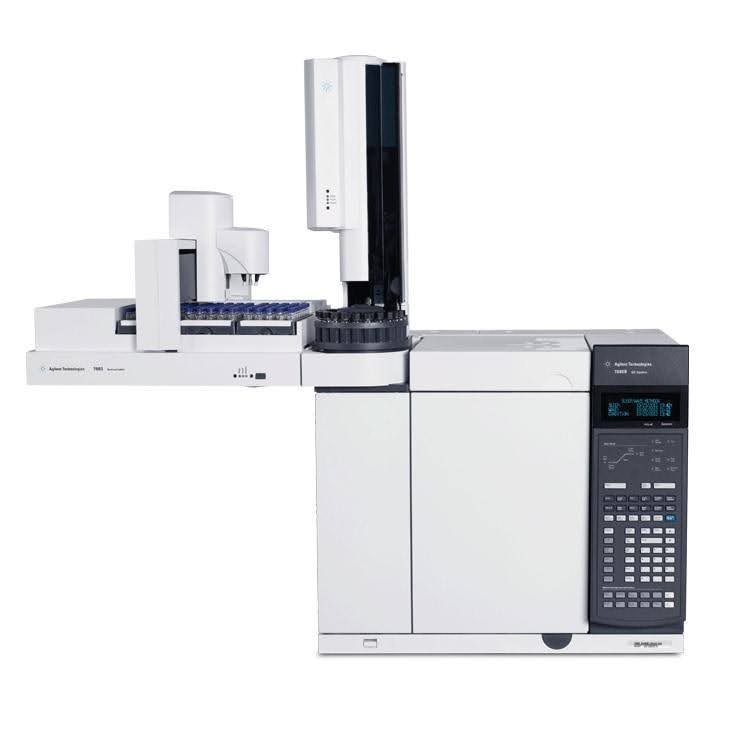
Figure 1 – Gas Chromatograph
Figure 2 – Schematic depiction of various fuel oxygenates peaks as analyzed by a gas chromatograph
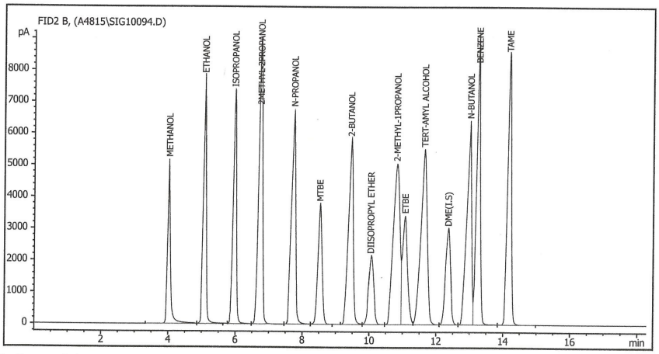
The driveability index is a measure of a gasoline’s performance across a number of operating conditions, covering cold start and warm-up operations. Its calculation incorporates elements of the distillation profile for the gasoline (10%, 50% and 90% evaporated distillation temperatures) identified by test method ASTM D86-23a as well as the gasoline’s ethanol content quantified by test method D4815-22.
The driveability index requirements for Colorado are summarized in Table 1.
Table 1 - Driveability Index (DI) Requirements for Colorado for gasoline containing 0-15 % of ethanol by volume.
Month | Maximum Driveability Index [°F] |
---|---|
January | 1220 |
February | 1230 |
March | 1230 |
April | 1250 |
May | 1250 |
June | 1250 |
July | 1250 |
August | 1250 |
September | 1250 |
October 1-15 | 1240 |
October 16-end | 1240 |
November 1-15 | 1240 |
November 16-end | 1230 |
December 1-15 | 1230 |
December 16-end | 1220 |
The octane number is a measure of the antiknock performance of a gasoline or gasoline component. The higher the octane number, the greater the fuel’s ability to resist engine knock. There are two types of octane numbers – the Research Octane Number (RON) and the Motor Octane Number (MON), which are based on different engine operating conditions. RON simulates low speed (idling), which affects low to medium speed knock. MON simulates higher speed (acceleration), which affects high-speed knock or ping. Octane number is not a measurement of a fuel’s power, but a measurement of the temperature at which the fuel ignites when compressed with a spark.
Both RON and MON are based on the knocking tendencies of pure hydrocarbons. n-heptane has an assigned value of zero and isooctane a value of 100. The octane number of a fuel is the percentage of isooctane in a blend with n-heptane that gives the same knock intensity as the fuel under test when evaluated under standard conditions in a standard engine.
Antiknock Index (AKI) is the average of RON and MON (or (R+M)/2), which is the number posted on gas station pumps (Figure 1).
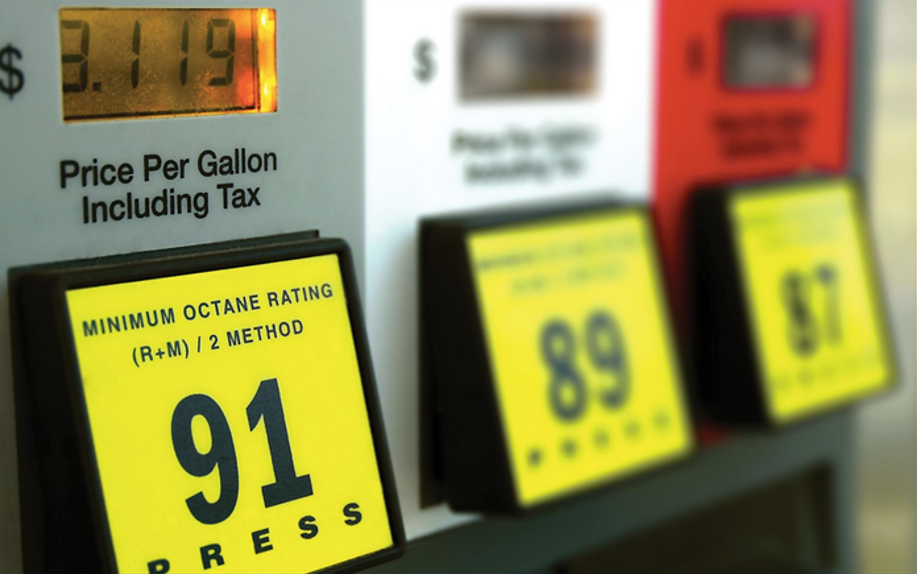
Figure 1 – The Antiknock Index (AKI) posted on gas station pumps
The Colorado State Fuel Quality Laboratory quantifies the knock ratings of engine fuels in accordance with ASTM D2699-24b and ASTM D2700-24c.
RON and MON of a spark-ignition engine fuel are determined using standard test engines (Figure 2) and operating conditions to compare its knock characteristics with those of reference fuel blends of known octane number. Compression ratio and fuel-air ratio are adjusted to produce a standard knock intensity for the sample fuel, as measured by a detonation measurement system.
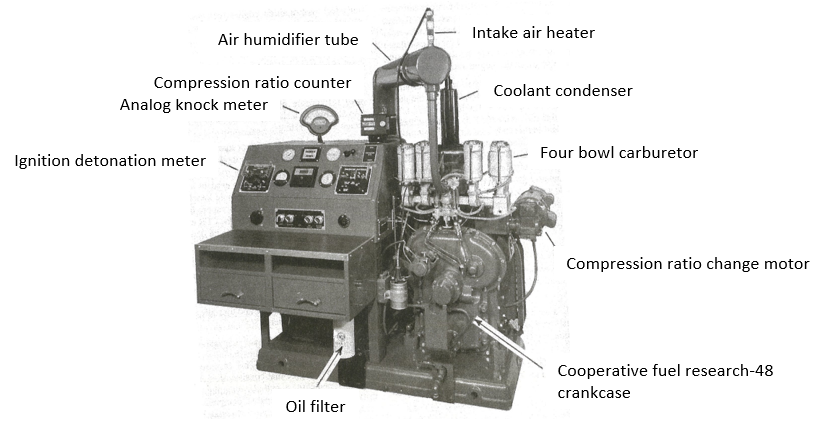
Diesel Analyses and Specifications
[Last revised 01/23/2024]
The State Fuel Quality Laboratory performs five ASTM approved analyses on each diesel fuel sample received from retail stations, and bulk plants located throughout the State of Colorado. In addition, the laboratory assesses the quality of diesel fuels in response to consumer concerns (Consumer Concern Form). All diesel fuels are sampled, handled and stored in accordance with ASTM D4840-99 and ASTM D4057-22.
ASTM D975-24 and ASTM D7467-23 prescribe the required properties of and appropriate test methods for different grades of (bio)diesel fuels, and include important information on seasonal and local (bio)diesel fuel requirements.
The analyses performed in the State Fuel Quality Laboratory are explained in the in the collapsible sections below.
To fulfill all essential quality requirements, the State Fuel Quality Laboratory has implemented and routinely performs a variety of Quality Control Checks and Quality Assurance Procedures in accordance with ASTM D6299-23a, ASTM D6792-23c, ASTM E882 and as defined in all ASTM Standard Test Methods. Additionally, the State Fuel Quality Laboratory participates in an International Quality Assurance Exchange Program – an interlaboratory proficiency testing program to evaluate laboratory performances, monitor test methods, personnel and reporting procedures on a monthly basis.
API gravity is a measure of how heavy or light a petroleum liquid is compared to water. Gravity is an important quality indicator for automotive fuels, where it affects storage, handling and combustion. Correlated with other properties, gravity can be used to give us an approximate hydrocarbon composition and heat of combustion.
The Colorado State Fuel Quality Laboratory follows ASTM D6822-24.
The API gravity is measured by reading a freely floating API hydrometer, and the temperature of the sample is read from a separate accurate thermometer in the sample (example of an API ThermoHydrometer below).
The observed hydrometer reading is corrected for various effects and reduced to the reference temperature (60 °F, 15.56 °C) by means of volume correction tables.

Flash point is an important property for assessing the overall flammability and combustion hazard of diesel fuels. At the Colorado State Fuel Quality Laboratory, testing following ASTM D56-22 is performed on all diesel fuel samples to measure their tendency to form a flammable mixture with air under controlled laboratory conditions.
A sample of diesel fuel is placed in the cup of the tester and, with the lid closed, heated at a slow constant rate. An ignition source is automatically directed into the cup at regular intervals. The flash point is the lowest temperature at which application of the ignition source causes the vapor above the sample to ignite. The minimum flash point of diesel fuels (for use in applications with conditions of varying speed and load) is 52 °C (or 125.6 °F). However, the flash point is waived to 38 °C (or 100.4 °F) during November through March when a Cloud Point standard of or below -12 °C (or 10.4 °F) is specified.
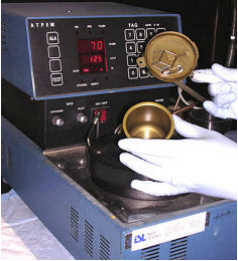
Figure 1 – Flash Point Tester at the State Fuel Quality Laboratory
The test method of determining the boiling range of a petroleum product by performing distillation has been in use for as long as the petroleum industry has existed. It is one of the oldest test methods under the jurisdiction of ASTM. The distillation (volatility) characteristics of hydrocarbons have an important effect on their safety and performance, especially in the case of fuels. The boiling range gives information on the composition, the properties, and the behavior of the fuel during storage and use. Volatility is the major determinant of the tendency of a hydrocarbon mixture to produce potentially explosive vapors. The distillation characteristics are critically important for automotive gasoline and diesel fuels, affecting starting, warm-up, drivability, dilution of the engine oil, fuel economy, carburetor icing and tendency to vapor lock at high operating temperature or at high altitude, or both. The distillation temperatures are used to characterize the volatility of diesel fuels and to determine whether the distillation properties meet the ASTM specifications (Table 1).
Table 1 – Distillation Temperature [°F] Requirements for (bio)Diesel Fuels at 90 % Evaporated at 101.3 kPa (760 mm Hg); Minimum 90 % recovered temperature is waived if cloud point is at or below 10.4 °F.
Minimum °F at 90% | Maximum °F at 90% | |
---|---|---|
Grade #1 | - | 442.4 |
Grade #2 | 539.6 | 640.4 |
Biodiesel | - | 649.4 |
The Colorado State Fuel Quality Laboratory follows ASTM D86-23a. A 100 mL sample is distilled under prescribed conditions for the specific fuel sample. The distillation is performed in a laboratory batch distillation unit (Figure 1) at ambient pressure. Systematic observations of temperature readings and volumes of condensate are made automatically. The volume of the residue and the losses are also recorded.
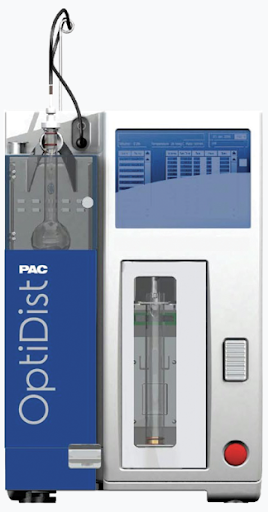
Figure 1 – Distillation Unit used at the Colorado State Fuel Quality Laboratory for the quantitative determination of boiling range characteristics of gasoline fuels
The Environmental Protection Agency (EPA) began regulating diesel fuel sulfur levels in 1993 due to air pollution concerns. Beginning in 2006, the EPA began to phase-in more stringent regulations to lower the amount of sulfur in diesel fuel to 15 milligram per kilogram (mg/kg). Based on ASTM D5798-21, the maximum allowable sulfur concentration in ethanol fuel blends (such as E85) is set at 80 mg/kg.
To determine the total sulfur content of automotive fuels, the Colorado State Fuel Quality Laboratory applies ASTM D4294-24 in accordance with ASTM D7343-20.
A diesel fuel sample is placed in an X-ray fluorescence spectrometer instrument (Figure 1) and exposed to a specific X-ray beam. This causes the sulfur to fluoresce so its concentration can be measured in mg/kg.
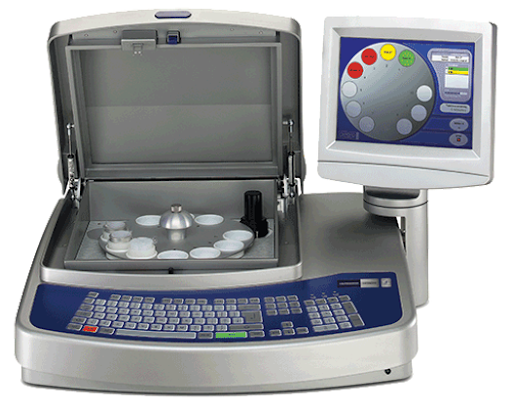
Figure 1 – XRF (X-ray Fluorescence) Spectrometer used at the Colorado State Fuel Quality Laboratory.
In diesel fuels, cloud point is the temperature at which the paraffin wax in the fuel forms crystals when cold. These wax crystals can collect in filters and eventually lead to blockage of automotive fuel systems. That is why cloud points must exceed seasonal and local minimum ambient air temperatures for the United States. Table 1 summarizes the minimum temperatures for Colorado.
Table 1 – Min. Ambient Temperatures for Colorado
Note: 105 longitude is approximately equivalent to the path of I-25.
Month | East of 105° [°C/°F] | West of 105° [°C/°F] |
---|---|---|
October | -2 / 28.4 | -8 / 17.6 |
November | -12 / 10.4 | - 18 / -0.4 |
December | - 14 / 6.8 | -25 / -13 |
January | -19 / -2.2 | -30 / -22 |
February | -15 / 5.0 | -24 / -11.2 |
March | -12 / 10.4 | -16 / 3.2 |
In compliance with ASTM D5771-21, the Colorado State Fuel Quality Laboratory determines the cloud point of diesel fuels with the apparatus shown in Figure 1.
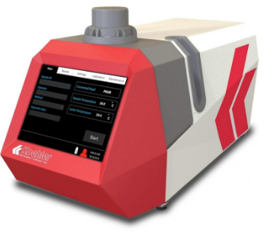
Figure 1 - Automatic Cloud Point Analyzer
The cloud point is determined by the automatic cloud point analyzer using an optical device for the detection of the crystal formation. After insertion of a test jar containing the diesel sample (Figure 2) into the analyzer, and the initiation of the program, the diesel sample is cooled incrementally. The sample is continuously monitored by a reflective optical system for the formation of a crystalline structure. When the crystallization of the wax in the diesel sample is detected by the optical system, the temperature is recorded. This test method can determine the temperature of the diesel sample at which wax crystals have formed sufficiently to be observed as a cloud with a resolution of 0.1 °C between -105 and 50 °C (-157 and 122 °F).
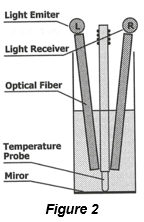
The cetane index is a figure which denotes the quality of a diesel fuel and refers to how quickly it can be ignited inside a compression setting. A higher cetane index indicates quicker combustion in the engine and a quieter, more smoothly running engine. A high cetane index also reduces harmful emissions from exhaust pipes, lessens wear and tear on batteries, engines and other automotive parts due to an improved distribution rate of lubricants.
Following ASTM D976-21e1, the Colorado State Fuel Quality Laboratory calculates the Cetane Index from the diesel fuel’s Gravity and Boiling Range. The Cetane Index is determined from the following equation:
Calculated Cetane Index = -420.34 + 0.016 G2 + 0.192 G log M + 65.01 (log M)2 – 0.0001809 M2
where:
G = API Gravity, determined by Test Method D287-22
M = Mid-boiling temperature, °F, determined by Test Method D86-23a and corrected to standard barometric pressure.
A minimum cetane number of 47 is required for diesel fuels.
Reformulated Gasoline (RFG)
As of May 1, 2024, gasoline sold in the Denver Metro and Northern Front Range (DM/NFR) area will have to be reformulated gasoline or RFG.
Why? Air pollution – primarily ground level ozone, the main ingredient in “smog”.
Back in 1970, Congress passed the Clean Air Act, which requires the Environmental Protection Agency (EPA) to set National Ambient Air Quality Standards (NAAQS) for six principal pollutants – one of which is ozone (40 CRF 50.10). Colorado has a lot of ozone precursor pollutants: volatile organic compounds (VOCs) and nitrogen oxides (NOx), produced by heavy vehicle traffic, oil & gas production, industrial emissions and wildfires. In addition, the terrain of the Denver Basin (Fig. 1) tends to trap and concentrate these pollutants. Add in the hot, sunny days of Colorado summers, and this creates ideal conditions for pollutants to chemically react in the atmosphere and produce ozone.
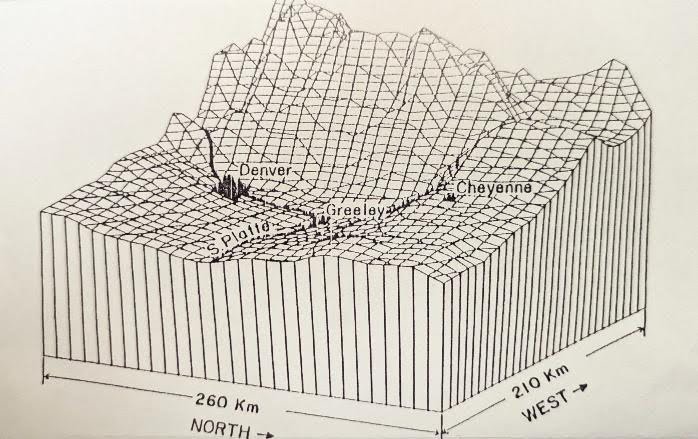
Due to these circumstances, ozone levels in the DM/NFR area were higher than the limits set by the EPA in 1997, and it was designated as a nonattainment area in April 2004 (Fig. 2). Since that time the DM/NFR area has not been able to meet the ozone standards EPA has set and has gone from being classified as “marginal” to “moderate” to “serious” in January 2020 under the standards set in 2008. Air quality in the area continued to decline and in November of 2022, the EPA reclassified the DM/NFR as a “severe” nonattainment area, triggering the requirement for RFG (40 CFR 1090.220).
What is it?
RFG is gasoline blended to burn more cleanly than conventional gasoline. It has the same components as conventional gasoline but is further processed and refined so that it produces less carbon monoxide and fewer VOCs. According to the EPA, areas that have participated in Phase I and Phase II of the RFG program have shown a reduction in these types of smog forming pollutants by approximately 27%. Additionally, RFG should not affect engine performance and is estimated to only cost 2-3 cents more per gallon to produce. Using RFG is another step to help improve Denver Metro and Northern Front Range air quality and bring ozone levels into compliance. Over 3.3 million Coloradans will breathe cleaner air due to the introduction of RFG.
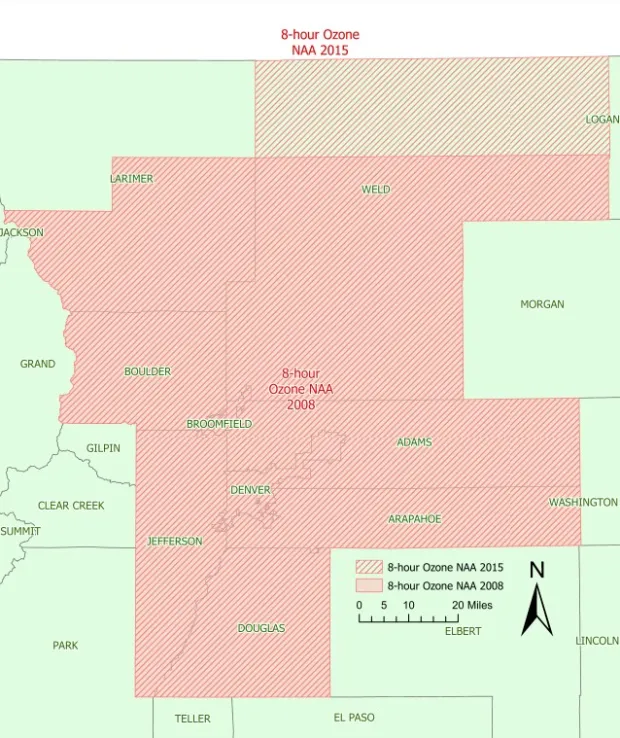
For more information about ozone and RFG you can visit:
Helpful Links
- American Petroleum Institute (API)
- American Society for Testing and Materials (ASTM)
- US Environmental Protection Agency (EPA)
- About Fuel Oxygenates
- Colorado Department of Public Health and Environment (CDPHE) Air Pollution Division
- Colorado Wyoming Petroleum Marketers Association
- International Quality Assurance Exchange Program
- NIST Handbook 44 – Specifications, Tolerances, and Other Technical Requirements for Weighing and Measuring Devices
- NIST Handbook 130 – Uniform Laws and Regulations in the Areas of Legal Metrology and Fuel Quality
- Colorado Code on Fuel Products